Success Stories
Successful collaborations
Since the launch of our inhalation component portfolio more than 30 years ago, our long-term partnerships with customers and industry players have resulted in a number of successful drug delivery devices being approved and launched in the global market. We have shaped the drug delivery device industry and led the way to improve patient outcomes in inhalation, injectable drug delivery and diagnostics. We are proud to share a selection of our successes.

Accelerating Device Development
In drug delivery device development and particular in prototyping, a challenge is to accelerate development timelines while delivering exceptional design accuracy at a low cost. The acquisition of the Origin One® P3™ DLP technology has enabled the New Product Development Centre at H&T Presspart to overcome this challenge.
The new technology allows H&T Presspart to create functional prototypes with very complex and precise geometries much faster and at a lower cost than with prototype moulds. With the P3™ DLP technology 3D prints have improved a lot:
- Surface finishes comparable to injection moulding
- Exceptional design accuracy and precision with tolerances smaller than 50 μm
- Excellent strength and rigidity of parts
“Every day we discover new Origin One® applications and materials, allowing us to remain at the forefront of design and development and we are doing today, which we thought was impossible yesterday,” – Paloma Herrera Director of Technology at H&T Presspart.
To learn more, please read our case study on the collaboration between H&T Presspart, Stratasys and Henkel.

Reconstitution Device Development
Our customer approached us with a basic principle drawing on a piece of paper and this is where H&T Presspart got involved. The idea was to develop a reconstitution device with the goal to transfer the liquid content from a cartridge into a container with lyophilized drug product, efficiently mix the two and then retransfer the solution back into the cartridge. The cartridge was then later to be used in an injection pen. The brief was to perform a proof of concept on a chosen design and industrialise the manufacturing.
The device comprised of 6 plastic components, sealing foils and a cannula and involved a multi-component injection and assembly process which was intended to be highly automated.
Our team performed design characterization tests, transport simulation and sterilisation studies to provide a proof of concept to the customer for a device which could subsequently be industrialised for high volume manufacturing.
One of the main challenges was to design a device which could be handled at low temperatures, and to avoid coring of stoppers at those temperatures. In addition, several cannula gauges, cannula tip geometries and post treatments of the grind had to be tested to find the optimal cannula solution for crimped vials.
For the industrialisation and in serial manufacturing, handling a double-beveled cannula was a complex undertaking which the teams could solve through a custom automation solution.
H&T Presspart delivered a concept which was successfully proven and ready for industrisation.

Parenteral Device Development
A global pharmaceutical customer approached H&T Presspart with the brief to design and develop a multi-component subcutaneous implanter device with retractable needle and needle safety features.
As part of a comprehensive development program and as input to the concept design phase, our team performed a detailed market study to analyze the current device landscape and relevant future market trends and regulatory requirements. A freedom to operate (FTO) study was also part of the initial concept phase.
Our customer chose a design concept from several different options that were generated and presented and our development team went on to optimize the design assuring the functionality and manufacturability of the device supported by comprehensive engineering studies, including simulations like Moldflow and Finite Element Method (FEM) analyses.
Throughout the development we produced prototypes to assess the different functions of the product and to fully characterize it, supporting the Design Freeze. Once first production batches were available we performed the Design Verification including sterilization tests and simulated the device in transport to ensure its robustness.
As a result of our development, H&T Presspart could successfully deliver GMP batches meeting all requirements for clinical studies to our customer.

Automation for Diagnostics
In 2016 our customer, a leading global healthcare company that develops medicines derived from plasma and other innovative biotech solutions approached H&T Presspart with an ambitious brief to produce a high-quality Diagnostic Gel card for blood group typing and investigation of antibodies. Our customer was looking for a second source to produce the gel card with high dimensional stability and impeccable cosmetic appearance for clear, consistent, and stable measurements in their labs.
Starting with the prototyping phase and development of low cavity tooling to demonstrate manufacturability, our teams worked in close partnership with the customer and managed the process design, scale-up and industrialisation and to deliver the product from a state-of the art manufacturing cell. Our regulatory affairs team supported the medical device technical dossier for successful regulatory submission.
With a strong focus on particle reduction the gel card is moulded and packaged in reusable boxes in a fully automated process without any operator manipulation. Through innovative tool design and material choices we could achieve very low cycle times.
We have implemented full statistical process control (SPC) to track cosmetic and dimensional parameters of the product and could achieve outstanding dimensional stability of the micro-tubes which was of highest priority for our customer.
With a production model to maximise capacity utilisation, implementing full automation and minimizing cell space we have been able to establish a sustainable business model and long-term partnership for mutual success.

In-vitro Equivalent Generics
A challenge to the inhalation industry is establishing in-vitro equivalence of a generic MDI with the Reference Listed Drug (RLD) product. A complex interaction between formulation and the device components, including dose counters, which have become mandatory in some markets, are making the development program a complex undertaking.
With our expertise in MDI components, our analytical laboratory and long-term customer relationships we understood early on that our customers would benefit from a holistic service to fast-track the registration of in-vitro equivalent MDIs with dose counters in regulated markets.
We have since set up a comprehensive program and have successfully developed generic in-vitro equivalent MDIs for originators such as Qvar®, Foster®, ProAir® and Flovent®.
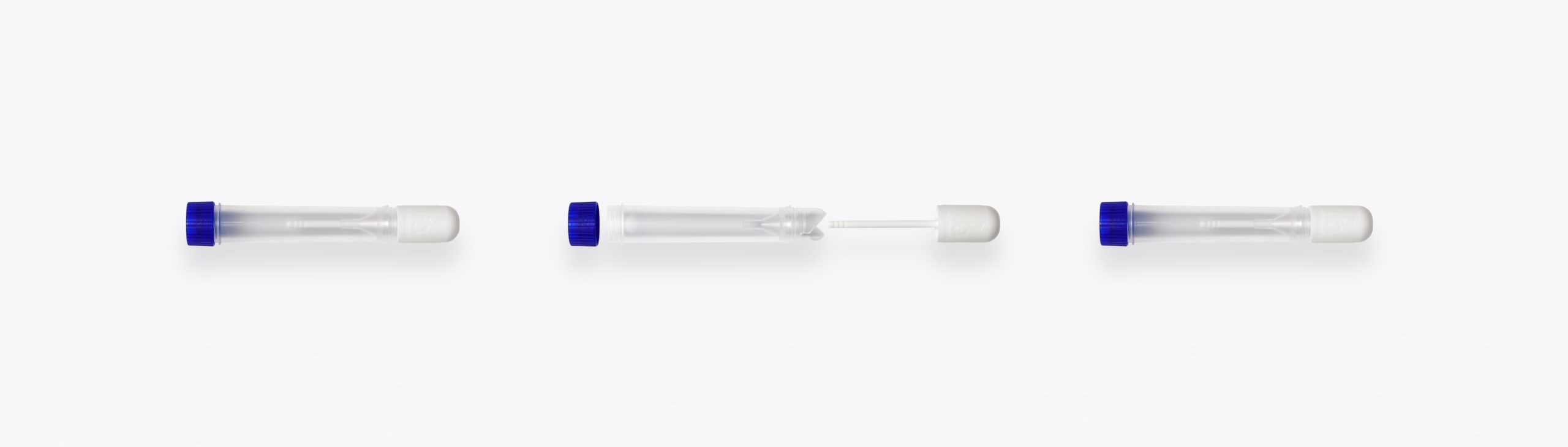
In-Vitro Diagnostics
Bühlmann Laboratories AG, a leading company in in-vitro diagnostics, approached H&T Presspart to develop two innovative diagnostic testing products for monitoring calprotectin’s, which are a key indicator of intestinal diseases such as Crohn’s disease and ulcerative colitis, in stool samples.
The aim of the project was to develop two user-friendly devices that would help patients collect the samples easily and cleanly and shorten the testing process.
A total of 8 pilot tools with different degrees of difficulty were produced for the prototype phase. One specific component, a 2-component valve lever with seal, was a particularly challenge when developing the tooling for the injection molding process. The filigree design (small contact surfaces and parts), the requirements for the materials and the condition of the component posed major challenges for our team of product designers and tool specialists. Finally, the valve lever with seal was successfully injected from an 8-cavity production tool.
During the product development phase, our team worked closely with the customer in formulating technical features (usability engineering), creating concepts and checking their feasibility, focusing on product designs, producing and checking the functionality and performance of prototypes through to concretization in a final design for series production. These individual steps were supported by appropriate quality assurance processes and by computer-aided programs (CAD, FEM, Moldflow).
With final customer approval on the design of the product and our manufacturing processes we were able to enter the industrialisation and mass manufacture phase for both products and ensure a timely and co-ordinate market launch.
“Following the acquisition, we welcome H&T Presspart as our partner in a long standing collaboration between Bühlmann and the Nidau site, and our joint commitment to focus on customers, quality and reliability.”
CEO, Bühlmann

Dispensing Actuators for CBD
Medical CBD drug delivery is one of the fastest growing segments of the pharmaceutical drug delivery market due to its potential in the treatment of a range of health conditions and chronic diseases. In 2020, Feather, a Canadian manufacturer and distributor of medical cannabis and CBD products, approached H&T Presspart for support in the development of a dispensing actuator for the delivery of CBD via the sublingual route.
Starting with a standard, H&T Presspart off-the shelf dispensing actuator, Feather’s initial tests with their formulation did not give the required spray pattern performance. Our product design team worked together with Feather to create a bespoke solution which meets the required product performance.
Based on our development, industrialization and tool-making capabilities and close collaboration between our companies we were able to provide a holistic service and successfully develop a suitable device covering all phases from design and prototyping to mass manufacturing.

Sunriser High Performance DPI Technology
A strong unmet need in dry powder delivery is a dry powder device which has low variability and high lung deposition of the delivered drug to the lung for a wide variety of different powders.
Particle engineering is one way to increase the efficiency of the delivered drug, another possibility is to increase the efficiency of the de-agglomeration process of the device, and when they both go hand in hand an ideal performance of the finished dry powder inhaler product can be achieved.
H&T Presspart has developed a highly efficient technology that delivers dry powder formulations with fine particle fractions higher than current marketed devices. The technology can handle different types of formulations such as classic carrier-based, spray-dried/carrier-based or spray-dried particles alone. Find out more in the attached case study.
H&T Presspart has developed a highly efficient technology that delivers dry powder formulations with fine particle fractions higher than current marketed devices. The technology can handle different types of formulations such as classic carrier-based, spray-dried/carrier-based or spray-dried particles alone.